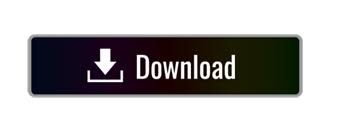
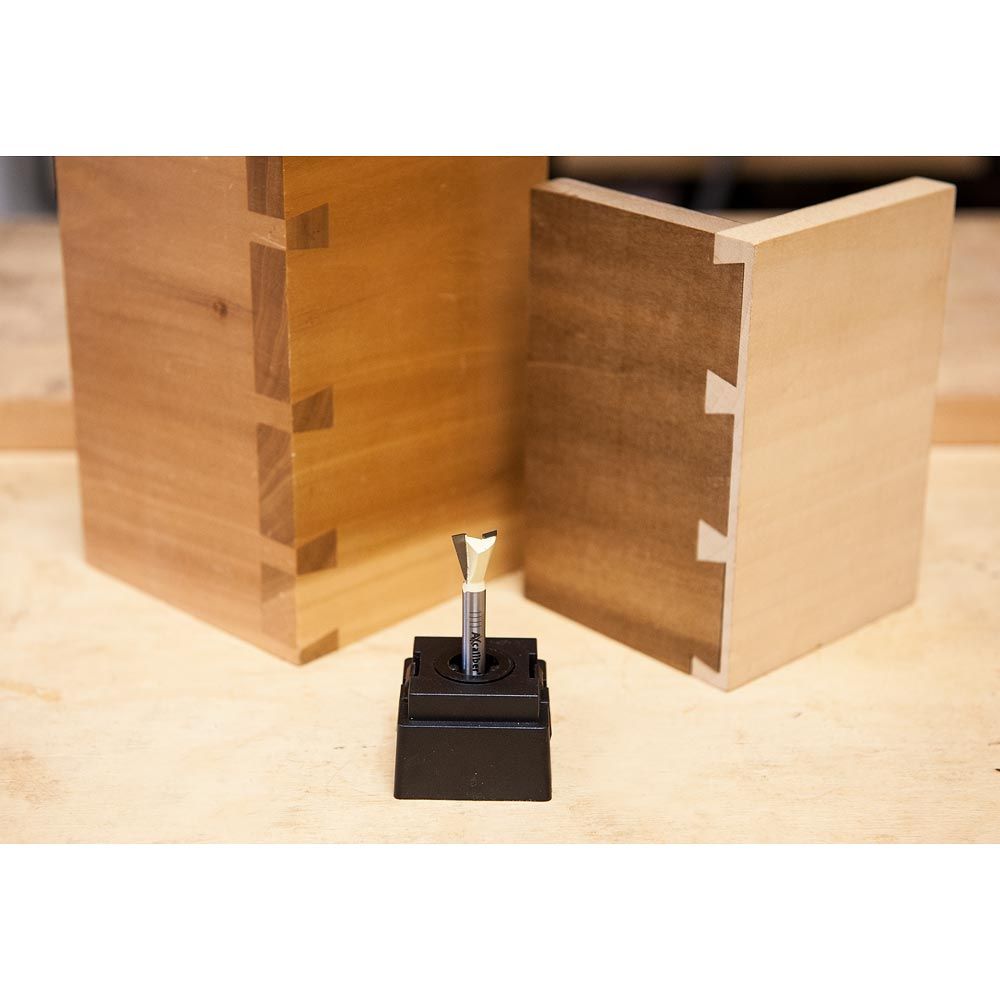
Thanks as always, this forum has been a lot of help. 08 deep shoulderĪny suggestions on where to go from here? I have milled a lot of aluminum, and if I was working with that I wouldn't be here. Shared album - Alex Crane - Google Photos I was hoping to get away with using this to mill the exposed surface in a later op. Seems to work OK but I think my surface finish leaves a bit to be desired.

I went with a 90 degree face mill since I need to do shoulder work as well. To be honest I was hoping for better surface finish. I got myself a 7 flute 2" face mill, and am using that for my initial face. Vancouver Wire EDM - Wire EDM MachiningAgree it could be like a fly cutter if it has proper clearance to the end and OD, and has some dish. It's just a holding dovetail so maybe the OP doesn't need to care, but if he has to change fucked up inserts all the time he'll care soon enough. So I concur that unless the tip rad is bigger than 0.020", a cut of that depth will be rougher than a badger's ass. Of greater concern, in my opinion, is whether the tips of the insert have a big enough radius to handle the DOC.Ī very small tip rad and a DOC that is bigger than that rad will encourage the inserts to act almost like a plow.pushing up a big bur and making the insert want to dive downward into the surface.Įven though the spindle bearings can handle it unless they're totally hooped, the finish is typically terrible as the cutter is forced downward into the finished surface. However as you correctly point out too, if the heel of the insert is hanging down, you will not get a flat surface.Īn insert tip hanging down is not that uncommon, but an insert heeling down would mean the cutter manufacturer fucked up the positioning of an insert pocket which I must believe is very rare. This is because the feedrate chosen assumes all the cutting load will be shared by all the inserts so if only one is cutting there will be swirl marks in the finish. It will also leave a crappier surface finish, but it will not fundamentally keep the cutter from doing its job. If an insert tip is protruding further than its mates the cutter will act like a flycutter and will lose the tip of that insert early. 0005 all the same you might use it to flatter the top. You might check the end to see clearance and dish and with that and with the end running. The pointier the points on the cutter, the less I want to load them.īut you're talking about making time on these, so you will have to accept a shittier dovetail cut in one go as a result and you'll have to change out your inserts more. This of course violates the rule of going balls out fast, but it's cheaper on inserts and it keeps the noise level down and makes a better dovetail too. So I take the extra time and walk down down the sidewalls in successive passes in order to preserve the cutter.
Cnc dovetail cutter full#
I've found that just plowing it into the side of the job at full depth makes both a shitty job and beats the cutter and the machine spindle to ratshit if the dovetail has any depth at all.Ī 0.050" deep dovetail is probably fine, even a 0.100 deep dovetail is probably fine but a 0.200 deep dovetail, especially an acute angle dovetail is hard on the cutter and often will wipe out the points in stainless steel, even babying the feedrate. It will also not face worth a shit if the points are sharp or close to it. If so, the cutter will be fragile and will not make many parts even in 303 SS before the points are gone.

Is this really what you hope to make, and does your cutter really have the dead sharp points necessary to mill this shape? First your dovetail as drawn in your picture show a sharp internal corner.
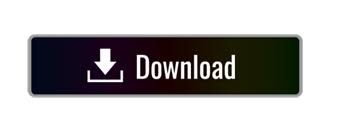